Cast-in-Place, Structural Concrete Framing
Selecting cast-in-place, structural concrete framing for your mid- or high-rise Wisconsin construction project provides benefits to everyone involved in the project, including the owner, specifiers, contractors, building occupants, and the community-at-large.
Advances in concrete technology and construction methods make structural concrete framing the smart choice in twenty-first-century Wisconsin. The use of today's reinforced, high-performance concretes provides a practical, cost-effective, aesthetically appealing, local material suitable for all mid- and high-rise building types, building bottom-line benefits across the entire life of your project - pre-construction, at-the-job site, and post-construction.
Pre-construction Benefits of Structural Concrete Framing
Selecting cast-in-place, structural concrete framing reduces both project startup time and start-to-finish construction schedules compared to other materials. With cast-in-place concrete, materials are readily available from local suppliers, permitting project planners to leverage just-in-time delivery efficiency. The availability of ready-mixed concrete can shave up to 20 weeks from "project-notice-to-proceed" to actual "construction-start." Cash-flow management also improves with structural concrete framing, as no outlay is required in advance of construction-start for material pre-ordering.
Structural concrete framing technology affords architects and engineers more versatility. Because a smaller footprint is required for buildings with structural concrete frames, projects can be constructed on smaller, confined job sites minimizing site disruption or expanding the use of available lands. In addition, less space is needed for staging during structural concrete framing construction adding flexibility for smaller sites and further reducing site disruption and investment costs.
At-the-Job Site Benefits of Structural Concrete Framing
Though perceptions persist that steel framing is faster than concrete, construction time-study data show once construction begins, 13 percent fewer delays are reported during structural concrete framing compared to steel.
In cast-in-place structural concrete construction, the project construction team has direct control of material scheduling and delivery logistics. Cast-in-place construction eliminates the time and cost of transporting prefabricated elements to the project and the time and cost of taking inventory and safely unloading and storing the heavy, prefabricated elements at the job site. Because ready-mixed concrete is manufactured and delivered as-needed, structural concrete framing technology reduces the size of construction site storage areas, minimizing site disruption.
Admixtures used in the manufacture of high-performance concrete for structural concrete framing help contractors overcome construction project challenges, so site-cast concrete construction can proceed quickly, year-round. These admixtures help contractors improve project quality, accelerate construction schedules, and reduce in-place concrete costs, including meeting early and/or ultimate strength requirements, overcoming pumping/material placement challenges, and supporting hot- or cold-weather construction.
With the newest generation of superplasticizing admixtures, high concrete strengths are achieved rapidly, and concrete placement on successive floors proceeds quickly, allowing other trades to install electrical, mechanical, plumbing, and HVAC systems and interior partitions on lower floors, as concrete structural framing work continues upward.
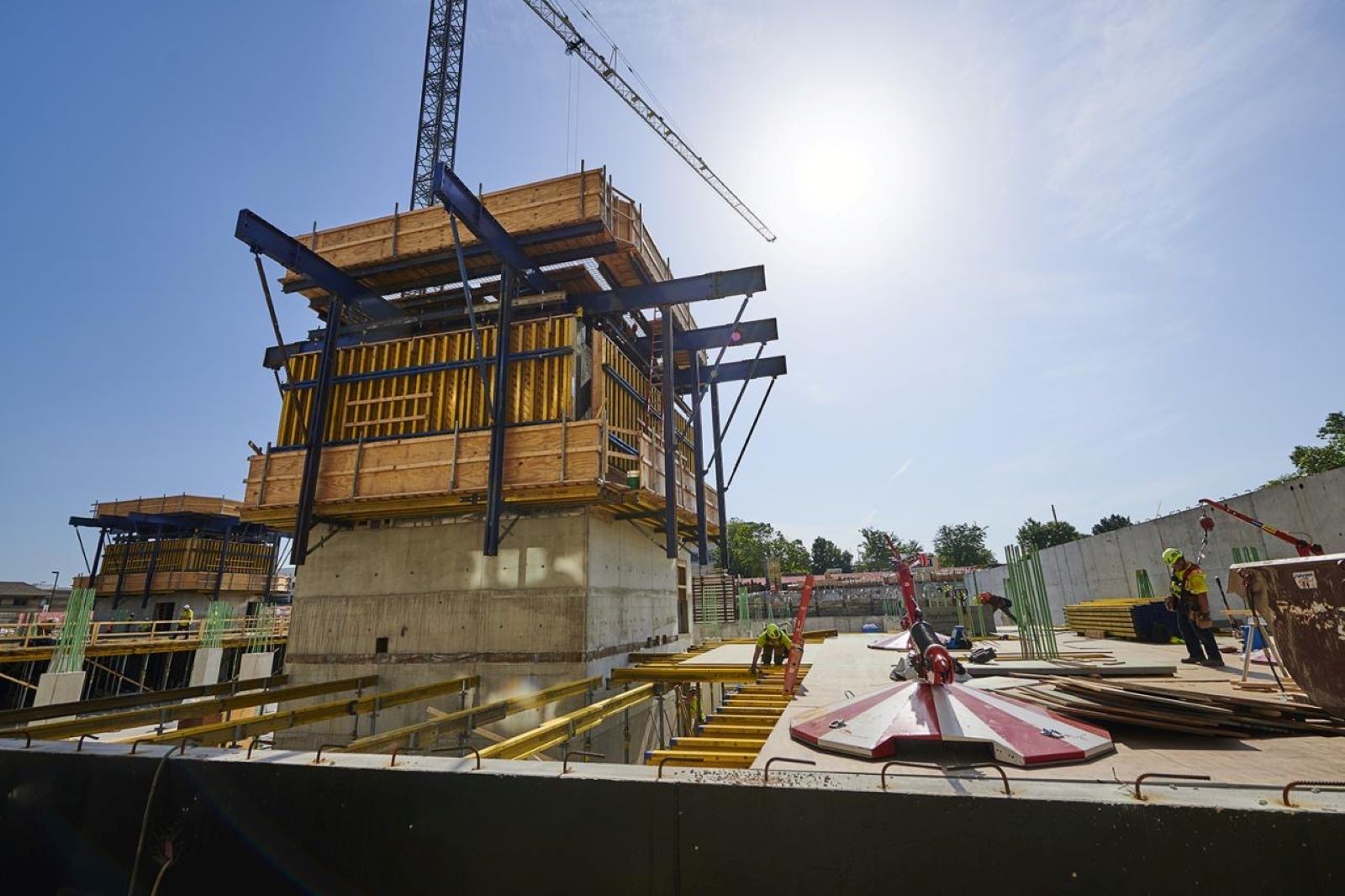
Post-Construction Benefits of Structural Concrete Framing
The high-performance mixtures and advanced construction techniques referenced above allow engineers and architects to design longer spans with fewer and smaller columns making more useable floor space available. Structural concrete also has a lower floor-to-floor height than steel or other framing materials, by up to two feet per floor, often permitting the addition of one or more additional stories for a given building height. By selecting structural concrete framing technology, two additional stories were added to the recently completed tenant options and project return on investment (ROI). Structural concrete framing technology allows developers to maximize marketable space, increasing tenant options, and project return on investment.
ROI continues long after construction is completed. Selecting cast-in-place, structural concrete framing provides developers, building operators, and tenants with a building that is quieter, stronger, safer, aesthetically pleasing, more energy-efficient, and easier and less expensive to maintain than buildings constructed with other structural framing material technologies.
Construction industry studies show compared to steel construction, concrete buildings have significantly decreased heating and cooling expenses, providing substantial savings for the life of the structure.
Advances in forming, texturing, and coloring technologies provide innovative options for architectural appeal and design versatility. Concrete accepts a variety of surface treatments and shapes, resulting in unique structures complementing any neighborhood. New coloring admixtures and stains provide attractive, economical alternatives to interior and exterior finishes.
Cast-in-place, structural concrete is one of the most fire-resistive building materials available, and buildings constructed with structural concrete framing technology typically qualify for reduced fire insurance rates. Should a fire occur, concrete walls and partitions effectively divide the structure into compartments, separating areas and limiting fire damage to specific compartments. Installed in conjunction with automatic sprinklers and smoke detectors, structural concrete framing systems provides an effective, multiple-phase, fire-defense system.
Because concrete can withstand catastrophic loading and there is less movement with concrete structures, buildings constructed with structural concrete framing technology have longer life expectancies. Concrete buildings are also wind and weather-resistant, require less maintenance, and have greater resale value than buildings constructed with other framing technologies.
Selecting cast-in-place, structural concrete framing provides sustainable solutions in key green building areas, including durability, acoustics, energy-performance and thermal mass, indoor air quality, recycled content use, and life-cycle balance.
Conclusion
Selecting a structural concrete framing systems for your mid- or high-rise Wisconsin construction project results in competitive initial construction costs, lower life-cycle costs over the service life of the structure, and lowest environmental impacts, including land and resource use, climate change, and health effects.
Ready-mix plants serve each of Wisconsin's 72 counties, all of Wisconsin's 1,259 towns, and every incorporated and unincorporated municipality in the state, employing local residents, fueling local economies, and contributing significant revenues to state and local community tax coffers. Additional local construction professionals, including formwork contractors, concrete finishers, rebar fabricators and placers, and other project vendors and suppliers, are convenient, quality-minded, as-needed, local sources of expertise, materials, equipment, and supplies for cast-in-place structural concrete framing construction.
From design, financing, scheduling, functionality, and performance to long-term risk exposure, structural concrete framing technology provides Wisconsin decision-makers of proposed mid- and high-rise buildings with a concrete solution meeting nearly all of a project's architectural, construction, and marketing needs. For these reasons, and for maximum economic and environmental benefit to the Wisconsin community the project will serve, your best choice for project structural framing is cast-in-place, structural concrete framing.